VOLK Roller Transporter at Hoesch Schwerter Profile
Steel profiles play an important role as structural elements and components in virtually all areas of the steel processing industry. The use of profiles offers among other advantages significant material savings and a reduction of machining rework costs.
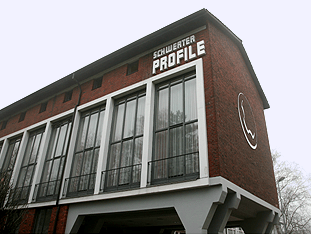
Hoesch Schwerter Profile GmbH specializes in the manufacture of special profiles
In practice, standard profiles are usually used which are mass-produced and thus relatively inexpensive. However, many construction or manufacturing problems can only be solved with special profiles. In these cases, the geometric shape of the profile is determined by the customer in accordance with his specific requirements and needs.
The customized manufacture of such special profiles is the core business of Hoesch Schwerter Profile GmbH. Approximately 720 employees at the Schwerte location produce profiles for the automobile, rail, material handling and construction industries, creating an anual turnover of almost 200 million Euros. About 60 percent of the production goes for export to customers located all over the world.
In the roller depot at Hoesch Schwerter Profile GmbH, hundreds of roller sets are stored – The surface contour of the rollers determines the geometric shape of the profile strand
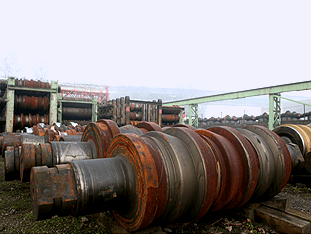
In the manufacture of the profiles, Hoesch uses various processes such as hot rolling and hot extruding. In the latter, after leaving the furnace, a steel billet is hydraulically pushed through a forming die using a ram with an extrusion force of 2.200 tons to form a profile strand.
While hot extrusion is primarily suited for highly complex profile shapes and small lot sizes, the forming technique of hot rolling is used in most other cases. Here red-hot iron billets, so-called slabs, are passed through two oppositely rotating rollers to form profile strands.
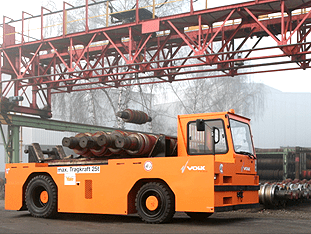
For transporting the rollers from the roller warehouse to the rolling mill, a VOLK Diesel Platform Truck DFW 25 is used – The vehicle features a load capacity of 25.000 kg
In the manufacture of the profiles, Hoesch uses various processes such as hot rolling and hot extruding. In the latter, after leaving the furnace, a steel billet is hydraulically pushed through a forming die using a ram with an extrusion force of 2.200 tons to form a profile strand.
While hot extrusion is primarily suited for highly complex profile shapes and small lot sizes, the forming technique of hot rolling is used in most other cases. Here red-hot iron billets, so-called slabs, are passed through two oppositely rotating rollers to form profile strands.
The rollers, which are arranged over each other in a rolling stand, have a diameter of up to 70 cm and a length of up to 2.8 meters. They are made of solid steel and weigh several tons. On the surface the rollers have a circumferential rib profile, whose contours in conjunction with the distance between the rollers in the rolling stand determine the geometric shape of the end product. In this way, an almost unlimited assortment of possible profile shapes can be produced with simple or complicated cross sections.
To provide for short reaction times and maximum flexibility here, the rollers are produced in the company’s own roller turning plant. Since a special roller set is produced for each profile cross section, hundreds of customized rollers at Hoesch Schwerter Profile GmbH must be stored and then transported on order to the rolling mill.
VOLK Roller Transporter DFW 25 in the rolling mill at Hoesch Schwerter Profile GmbH – In the foreground, two giant rollers each weighing several tons can be seen
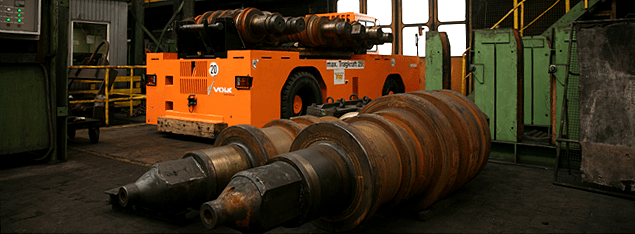
For the transport of the rollers, which weigh several tons, a VOLK Diesel Platform Truck of the type DFW 25 is used. The loading area features dimensions of 4.20 m x 2.50 m and is equipped with a special transport rack to hold the rollers. The sturdily constructed vehicle has two high-quality Kessler axles to provide for sufficient reserves when transporting heavy loads of up to 25.000 kg.
A powerful Deutz diesel engine with a cubic capacity of more than four liters ensures that the vehicle can reach a speed of 15 km/h even under maximum load. Surmounting a nine percent incline at the factory site is also no problem for the roller transporter. The required traction is provided by the vehicle’s heavy empty weight of 8.000 kg and two pairs of rear tires in the giant format 10.00 – 20.
In spite of its large dimensions, the vehicle has an amazingly small turning radius of only 7.12 m. Shunting in tight spaces is made easier with hydraulic power steering and a very sensitive hydrostatic drive. A video rear-view system ensures that the driver always has optimum visibility to the rear side of the vehicle – even when carrying bulky loads on the loading area. This is especially important in the Hoesch Schwerte plant which has organically grown over decades, thus resulting in some constructional bottlenecks.

VOLK Fahrzeugbau GmbH
Stahlstraße 15
88339 Bad Waldsee
+49 7524 9709 0
info@volk.de